
- Mar 28, 2022
Causes and Treatment Methods of EDM Molybdenum Wire Breakage
EDM Molybdenum wire plays a vital role in the high speed and medium speed cutting processing. High-strength, low-elongation molybdenum wire is the guarantee of high efficiency and high stability processing. However, it is inevitable to encounter the problems of broken wire, burnt wire, and speckled wire in the actual processing process, we have summarized the following common phenomena and corresponding solutions.
A. Analysis and Solutions of Broken Wire Phenomenon
1. Broken wire caused by power feed contact
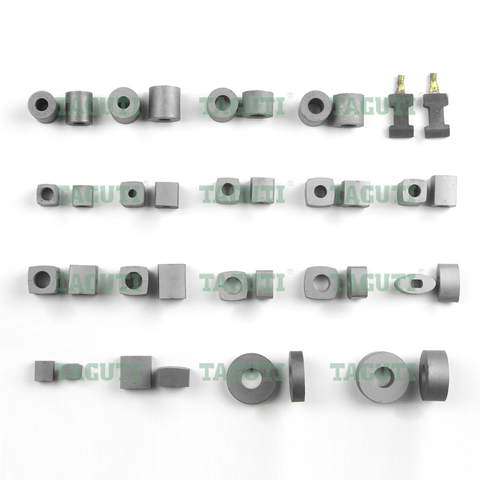
The molybdenum wire for EDM runs for a long time and contacts the power feed contact, resulting in groove marks on it. The EDM molybdenum wires are pinched off due to the excessively large groove marks caused by not treating the groove marks for a long time
Solution: Regularly rotate the power feed contact by a certain angle, move it horizontally or replace it with a new one.
2. Broken wire caused by EDM Guide Wheel
The EDM molybdenum wire is guided by the EDM Guide Wheel, the accuracy of it will affect the operation of the EDM molybdenum wire, and the axial and radial runout of the cutting machine wheel bearing will affect the accuracy of the electric discharge machining of the molybdenum wire and surface finish of workpiece, even broken wires.
Solution: Maintenance of EDM guide wheel requires regular injection of grease. When its service life is reached, it must replace the bearing or the guide wheel pulley assembly.
3. Broken wire caused by installing and tightening
If the tensioning force is too large when installing, it may also cause wire breakage. If the force is too small when tightening, the tension of the EDM molybdenum wire will be insufficient; the wire is pulled, resulting in broken wire.
Solution: It needs to choose high-quality,high-strength, low-elongation molybdenum wire for EDM , and adjust the appropriate strength to wire and tighten the wire.
4. Broken wire caused by the wire drum
During the processing, the wire drum continuously moves left and right. If the wear is serious, its radial runout will cause the tension change of the EDM molybdenum wire during the cutting process, which will cause the overlapping of the wire, resulting in broken wire.
Solution: It is necessary to regularly check the accuracy of the wire drum and adjust the gap.
5. Broken wire caused by unreasonable winding of EDM molybdenum wire on the wire drum
It needs to reserve 5-10mm wires in the two sections of the wire drum, otherwise it is easy to break the EDM molybdenum wire during reversing.
Solution: Reasonably reserve molybdenum wire for EDM when threading.
6. Broken wire caused by the failure of the reversing switch
The switch pressure plate is not fixed, or the travel switch is not pressed down, or the travel switch fails.
Solution: Check the workability of the reversing switch and the switch pressure plate before the wire cutting process.
7. Broken wire caused by EDM molybdenum wirenot installed properly
If the molybdenum wire for EDM is not installed on the correct wire path during wire feeding, such as outside the EDM guide wheel, outside the power feed contact, outside the EDM nozzle, etc., it will be broken when the machine is turned on.
Solution: After the wire is installed properly, check the path and see if it is on the correct wire path.
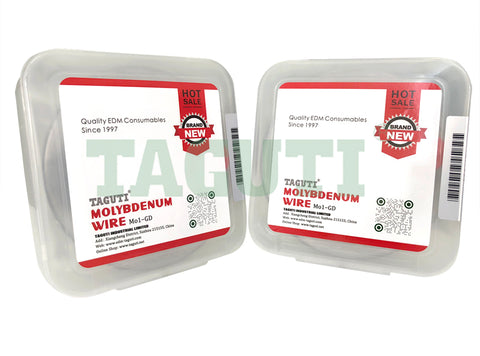
8. Broken wire caused by thermal expansion and contraction of EDM molybdenum wire
If the molybdenum wire for EDM is not parked on both sides of the wire drum after processing, it will be broken after cooling if the tension of the molybdenum wire is too tight.
Solution: After stopping, the EDM molybdenum wire should stop at one end of the wire drum.
B. Analysis and Solutions of Wire Burning Phenomenon
1. Machine tool: Excessive wear of HS-EDMparts, resulting in too much vibration of EDM molybdenum wire, etc.
2. Electric cabinet: Too large current, too small pulse interval ratio, secondary discharge, leakage of machine tools, poor insulation, etc.
We start from these two aspects to investigate one by one:
a. HS-EDM parts inspection
1. EDM guide wheel: Check the front and rear guide wheels of the machine tool, if there is shaking, it must be replaced.
2. Power feed contact: Check whether it is excessively worn or has grooves, which will cause the wire to be stuck; check whether the contact between the EDM molybdenum wireand power feed contact is normal, and whether there is obvious spark discharge.
3. Wire conveying system: Check whether the transmission of the wire conveying system is stable. If the wire drum jumps or the wire is unstable, the EDM molybdenum wirewill vibrate abnormally.
b. Check the mechanical parameters of the EDM machine tool
The perpendicularity and parallelism between the EDM guide wheel and the wire drum, and the parallelism between the Y axis of the worktable and the wire drum should be less than 0.02mm according to the design requirements.
c. Check the electrical cabinet
1. Excessive current
If the current is too large during processing, it is easy to cause wire burning.
2. The pulse interval is too small
If the pulse interval is too small during processing, it is easy to cause wire burning during the secondary discharge.
3. High-frequency voltage
When the high-frequency voltage is unstable and exceeds ±10% of the set voltage of the electric cabinet system, wire burning will easily occur.
C. Filament Definition, Analysis and Solutions
After a period of cutting, the EDM molybdenum wire will have black spots, which are usually several to ten millimeters long, and the intervals between the black spots are usually several to tens of centimeters. These dark spots are burnt and carbonized after a period of continuous arcing. The molybdenum wire for EDM becomes thin, brittle and carbonized, then it is easy to break. The black spots form black spots on the wire tube, sometimes they are arranged according to a certain regular rate to form patterns, so they are called "speckled wire".
The speckled wire produced on the EDM Molybdenum wire mainly has the following three elements:
1. The output quality of the pulse signal of the pulse power supply, especially the aging of old equipment and electronic components, is prone to distortion of the pulse signal.
Solution: It is necessary to use an oscilloscope to detect the waveform, pulse width, and interval ratio, and replace the aging components.
2. Pay attention to the state of EDM Gel, the working fluid is too dirty, the concentration is too low, etc., which hinders the insulation stability of the discharge medium.
Solution: Replace with new EDM Gel.
3. The thickness of the processing workpieceis too thick, the processing parameters are improperly selected, and the jet flow of the EDM Gel is not good (the amount of gel is small, the gel does not enter the slit effectively, etc.), so that the metal residue is not easy to discharge. In particular, the surface of the workpiece has oxide skin, forging interlayers, and the raw materials are quenched without forging and tempering, which has a high probability of causing the filigree phenomenon of wire-cut EDM molybdenum wire